What is Porosity in Welding: Necessary Tips for Getting Flawless Welds
Wiki Article
The Science Behind Porosity: A Comprehensive Overview for Welders and Fabricators
Understanding the intricate systems behind porosity in welding is essential for welders and makers making every effort for impeccable workmanship. As metalworkers explore the depths of this phenomenon, they reveal a globe regulated by numerous variables that influence the formation of these minuscule gaps within welds. From the structure of the base materials to the complexities of the welding process itself, a multitude of variables conspire to either exacerbate or relieve the presence of porosity. In this comprehensive overview, we will certainly decipher the scientific research behind porosity, exploring its results on weld top quality and unveiling progressed techniques for its control. Join us on this trip via the microcosm of welding blemishes, where precision meets understanding in the pursuit of flawless welds.Recognizing Porosity in Welding
FIRST SENTENCE:
Assessment of porosity in welding exposes crucial insights into the honesty and high quality of the weld joint. Porosity, identified by the visibility of cavities or gaps within the weld steel, is a common issue in welding processes. These spaces, if not appropriately resolved, can endanger the structural stability and mechanical buildings of the weld, leading to prospective failings in the ended up product.
To find and quantify porosity, non-destructive screening approaches such as ultrasonic screening or X-ray inspection are usually utilized. These methods enable the recognition of inner defects without endangering the integrity of the weld. By examining the size, shape, and circulation of porosity within a weld, welders can make enlightened choices to boost their welding processes and attain sounder weld joints.
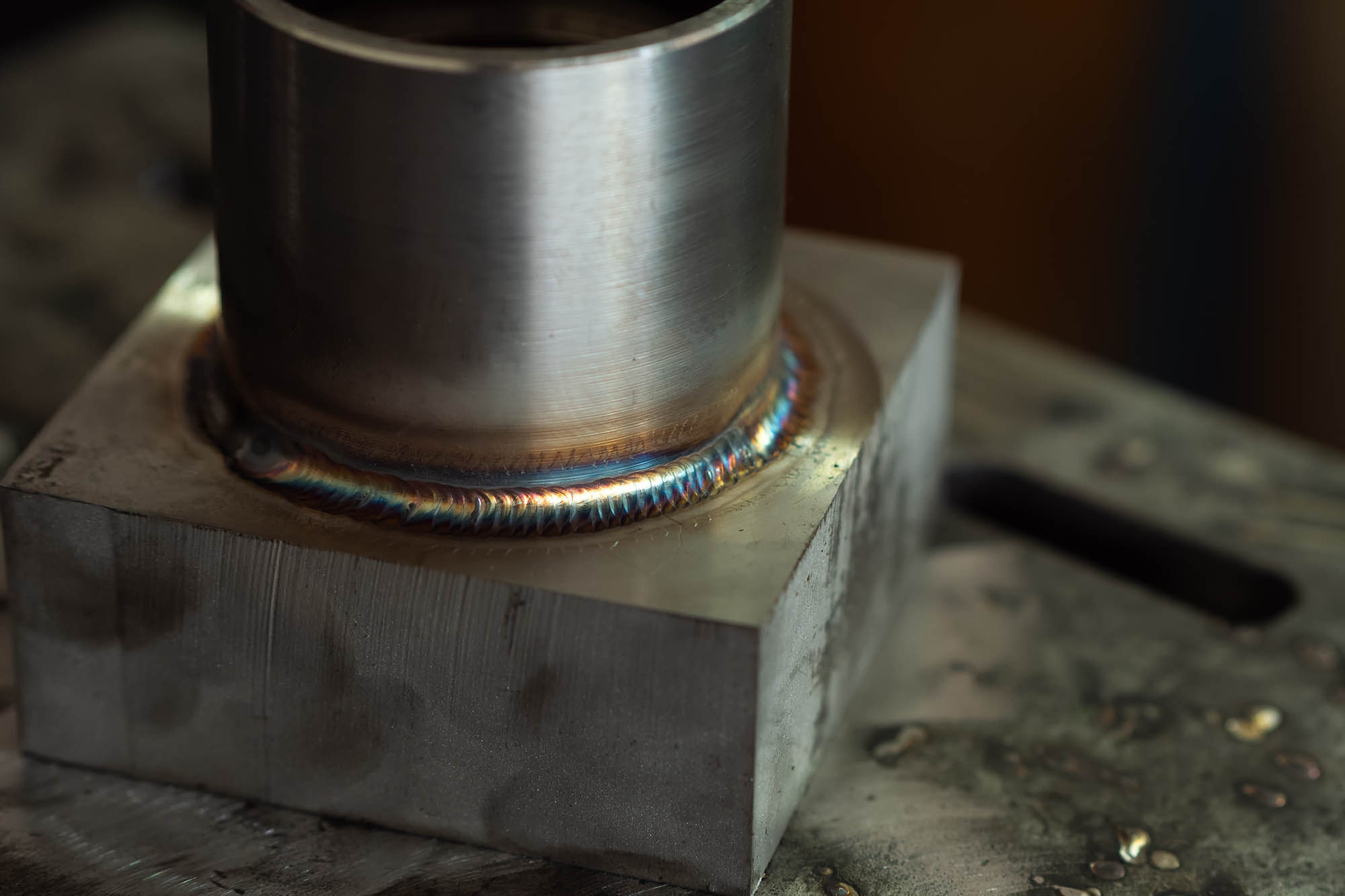
Aspects Influencing Porosity Formation
The incident of porosity in welding is affected by a myriad of elements, ranging from gas shielding efficiency to the complexities of welding criterion setups. Welding criteria, consisting of voltage, existing, take a trip speed, and electrode type, also effect porosity formation. The welding technique employed, such as gas steel arc welding (GMAW) or protected steel arc welding (SMAW), can affect porosity development due to variants in warm circulation and gas protection - What is Porosity.Effects of Porosity on Weld High Quality
Porosity formation significantly compromises the structural integrity and mechanical residential or commercial properties of bonded joints. When porosity exists in a weld, it creates gaps or tooth cavities within the product, lowering the total toughness of the joint. These spaces act as stress focus points, making the weld more at risk to splitting and failure under lots. The presence of porosity additionally weakens the weld's resistance to rust, as the trapped air or gases within deep spaces can react with the surrounding setting, causing degradation gradually. Additionally, porosity can prevent the weld's ability to hold up against pressure or influence, further endangering the overall high quality and integrity of the welded framework. In crucial applications such as aerospace, auto, or structural building and constructions, where safety company website and longevity are critical, the destructive effects of porosity on weld high quality can have extreme consequences, highlighting the significance of lessening porosity via appropriate welding methods and treatments.Techniques to Minimize Porosity
Furthermore, making use of the suitable welding criteria, such as the appropriate voltage, existing, and travel rate, is crucial in stopping porosity. Maintaining a constant arc size and angle during welding additionally assists lower the chance of porosity.
Moreover, selecting the appropriate securing gas and maintaining appropriate gas circulation rates are necessary in minimizing click to read porosity. Utilizing the ideal welding technique, such as back-stepping or utilizing a weaving movement, can also help disperse warm evenly and reduce the chances of porosity formation. Finally, making certain appropriate ventilation in the welding setting to eliminate any potential sources of contamination is crucial for attaining porosity-free welds. By applying these strategies, welders can effectively lessen porosity and produce high-grade welded joints.
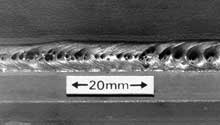
Advanced Solutions for Porosity Control
Executing sophisticated innovations and cutting-edge methods plays a critical duty in achieving remarkable control over porosity in welding procedures. useful reference Additionally, utilizing innovative welding techniques such as pulsed MIG welding or modified environment welding can additionally help reduce porosity problems.An additional advanced solution includes the use of innovative welding tools. As an example, utilizing equipment with built-in functions like waveform control and sophisticated power resources can boost weld top quality and reduce porosity risks. In addition, the execution of automated welding systems with specific control over criteria can significantly reduce porosity problems.
Additionally, incorporating advanced surveillance and examination innovations such as real-time X-ray imaging or automated ultrasonic screening can help in finding porosity early in the welding procedure, permitting for prompt corrective activities. Generally, incorporating these innovative options can substantially enhance porosity control and enhance the total high quality of welded parts.
Final Thought
To conclude, understanding the scientific research behind porosity in welding is necessary for welders and producers to produce high-grade welds. By determining the factors affecting porosity formation and applying methods to minimize it, welders can enhance the total weld high quality. Advanced solutions for porosity control can better enhance the welding process and make certain a strong and reliable weld. It is essential for welders to continually inform themselves on porosity and implement best techniques to achieve optimum results.Report this wiki page